A Biased View of Alcast Company
A Biased View of Alcast Company
Blog Article
Alcast Company for Dummies
Table of ContentsAlcast Company for Beginners10 Easy Facts About Alcast Company ExplainedAn Unbiased View of Alcast CompanyWhat Does Alcast Company Do?An Unbiased View of Alcast CompanySome Known Details About Alcast Company
Chemical Contrast of Cast Aluminum Alloys Silicon promotes castability by minimizing the alloy's melting temperature and improving fluidness during casting. Additionally, silicon contributes to the alloy's toughness and put on resistance, making it beneficial in applications where resilience is crucial, such as auto components and engine parts.It also enhances the machinability of the alloy, making it simpler to refine into finished products. In this means, iron adds to the total workability of light weight aluminum alloys.
Manganese adds to the stamina of light weight aluminum alloys and boosts workability (aluminum casting manufacturer). It is commonly used in wrought light weight aluminum items like sheets, extrusions, and profiles. The visibility of manganese aids in the alloy's formability and resistance to splitting throughout manufacture processes. Magnesium is a lightweight element that supplies toughness and impact resistance to light weight aluminum alloys.
Alcast Company Can Be Fun For Everyone
Zinc boosts the castability of aluminum alloys and aids manage the solidification process during casting. It enhances the alloy's toughness and hardness.
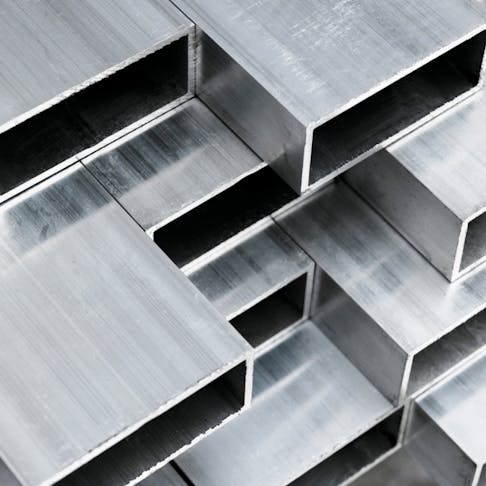
The main thermal conductivity, tensile stamina, yield toughness, and prolongation differ. Amongst the above alloys, A356 has the highest possible thermal conductivity, and A380 and ADC12 have the cheapest.
Alcast Company Fundamentals Explained
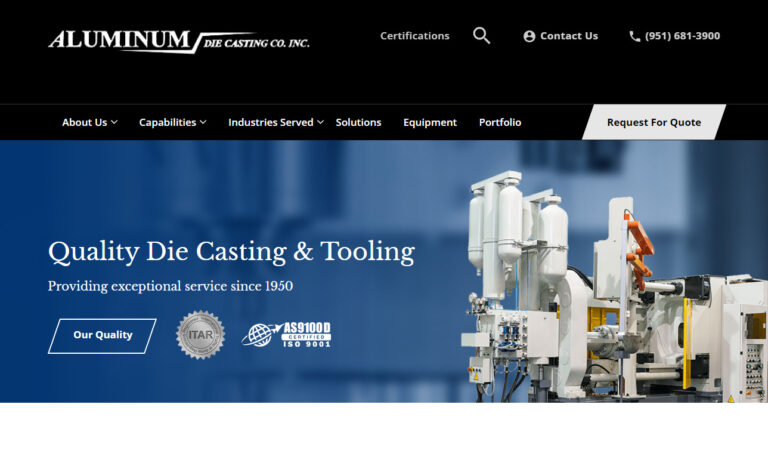
In precision casting, 6063 is fit for applications where intricate geometries and top notch surface coatings are paramount. Examples include telecommunication enclosures, where the alloy's exceptional formability permits streamlined and aesthetically pleasing layouts while keeping architectural integrity. Likewise, in the Lighting Solutions sector, precision-cast 6063 elements create elegant and effective lights fixtures that call for intricate shapes and excellent thermal efficiency.
The A360 shows remarkable prolongation, making it optimal for complicated and thin-walled elements. In precision casting applications, A360 is fit for markets such as Customer Electronics, Telecommunication, and Power Devices.
The Definitive Guide for Alcast Company
Its distinct residential or commercial properties make A360 a beneficial choice for accuracy casting in these industries, improving item resilience and top quality. aluminum casting company. Aluminum alloy 380, or A380, is an extensively used casting alloy with a number of distinct features.
In precision spreading, aluminum 413 shines in the Customer Electronic Devices and Power Tools industries. This alloy's exceptional rust resistance makes it a superb choice for exterior applications, guaranteeing durable, resilient products in the discussed sectors.
The Basic Principles Of Alcast Company
The aluminum alloy you select will considerably influence both the spreading process and the buildings of the final item. Due to the fact that of this, you need to make your choice carefully and take an enlightened method.
Establishing one of the most appropriate aluminum alloy for your application will indicate evaluating a large Check This Out variety of features. These relative alloy characteristics comply with the North American Pass Away Spreading Organization's standards, and we have actually separated them right into two categories. The first classification addresses alloy characteristics that impact the manufacturing procedure. The second covers qualities influencing the residential properties of the end product.
The Greatest Guide To Alcast Company
The alloy you choose for die spreading directly influences numerous aspects of the casting process, like just how very easy the alloy is to deal with and if it is prone to casting flaws. Warm fracturing, likewise understood as solidification cracking, is a common die casting issue for aluminum alloys that can result in internal or surface-level tears or cracks.
Certain aluminum alloys are much more at risk to warm breaking than others, and your choice must consider this. It can harm both the cast and the die, so you ought to look for alloys with high anti-soldering homes.
Rust resistance, which is currently a significant attribute of aluminum, can vary significantly from alloy to alloy and is a necessary particular to consider relying on the environmental conditions your item will be subjected to (Casting Foundry). Put on resistance is an additional building commonly sought in light weight aluminum items and can separate some alloys
Report this page